The typical wind turbine blade in the field today is made with traditional composite materials, such as fiberglass infused with an epoxy thermoset resin.
Because this approach is energy intensive, costly, and nonrecyclable, National Renewable Energy Laboratory (NREL), has been experimenting with groundbreaking thermoplastic resins.
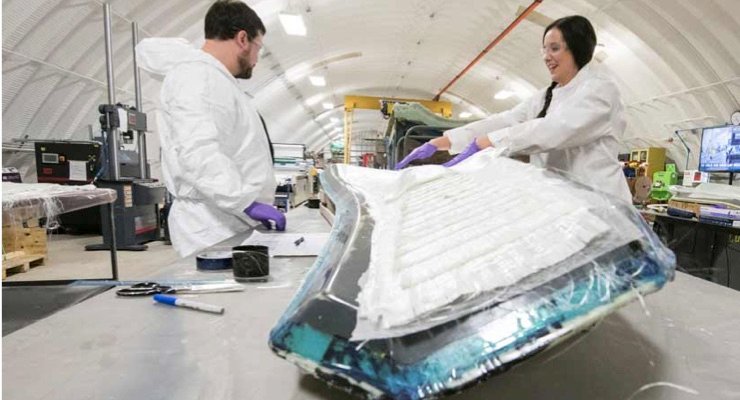
Thermoplastic composites hold the potential for enabling lighter-weight and lower-cost blades that can be recycled at the end of their lifetimes.
With $75,000 in funding from the U.S. Department of Energy Water Power Technologies Office’s Water Power Laboratory Seedling Program, the researchers began a year-long effort to use 3D-printing and thus combine additive and composite manufacturing techniques into a faster, cheaper, and more repeatable process.
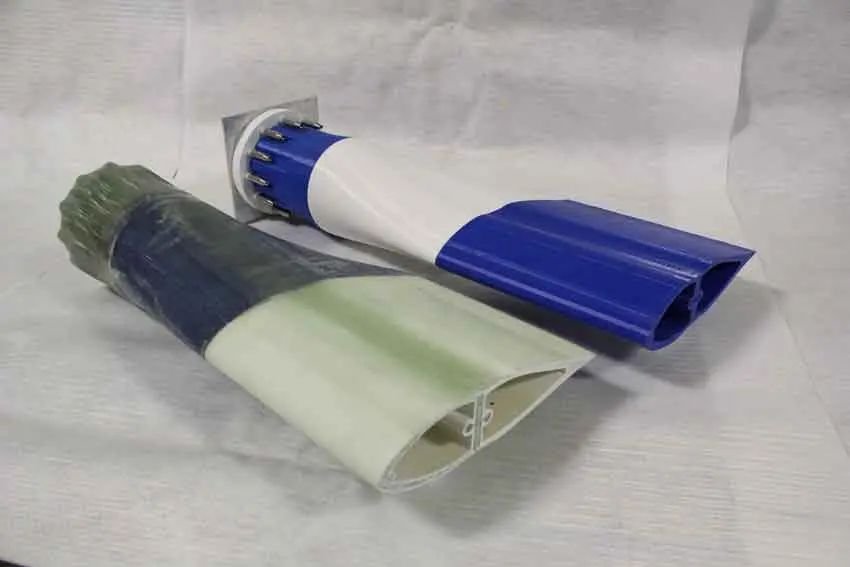
For the project, researchers created an additively manufactured internal molds that could become a permanent part of the final load-bearing structure.
Though other industries have regularly used internal molds for composite manufacturing, they are rarely left as part of the final structure. And this approach had not yet been demonstrated in the renewable energy industry.
The team demonstrated unique design features that could lead to improvements in manufacturability, blade strength, reliability, and continuity, such as integrated fasteners and resin passageways.
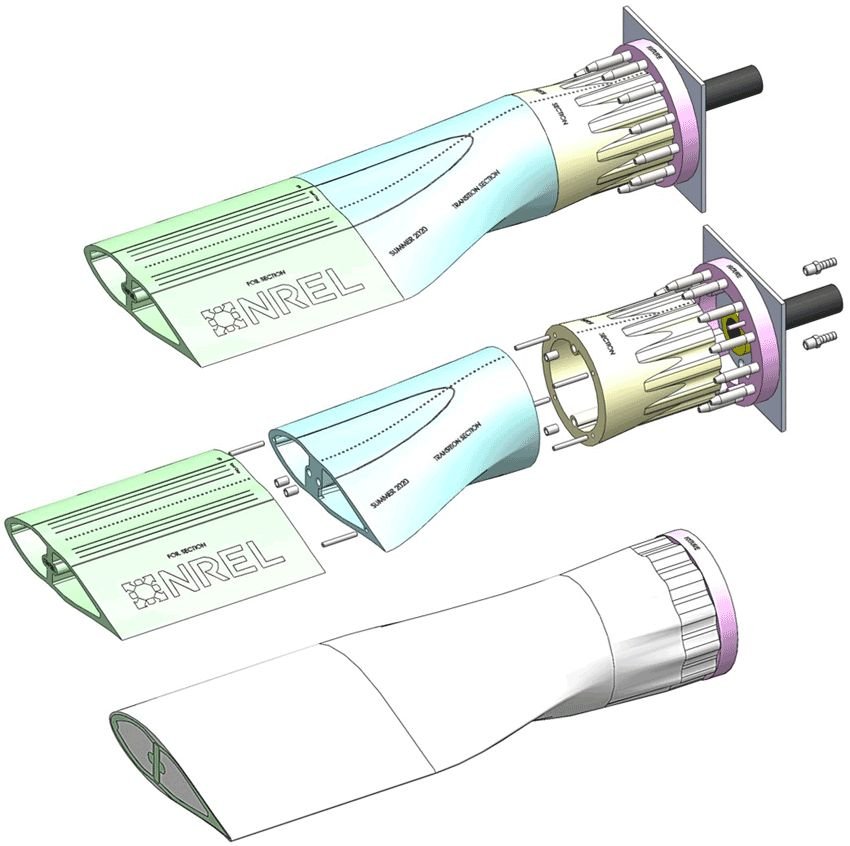
NREL 3D-printed the tidal turbine blade mold in four sections and then wrapped composite plies around them to remove any discontinuities and eliminate common points of failure.
NREL saw an opportunity to combine the strengths of additive manufacturing with advanced composite materials for more efficient device prototyping.
The Seedling project identified several opportunities to improve the tidal turbine blade manufacturing process, including single-piece construction and embedded root fasteners.
Most significantly, the researchers were able to demonstrate that additively manufactured composite molds can serve as part of the final load-bearing structure.
This is a syndicate News Feed; edited by Clean-Future Team