Researchers at the Department of Energy’s Oak Ridge National Laboratory have developed a automated robotic disassembly system for spent electric vehicle battery packs to safely and efficiently recycle and reuse critical materials while reducing toxic waste.

Whether a recycler simply wants to get through the outer housing to access batteries and replace worn components, or completely recycle battery stacks for recovery of cobalt, lithium, metal foils and other materials, the first step is battery diagnostics for safe and efficient handling and disassembly.
Limiting human interaction is important for both safety and efficiency.
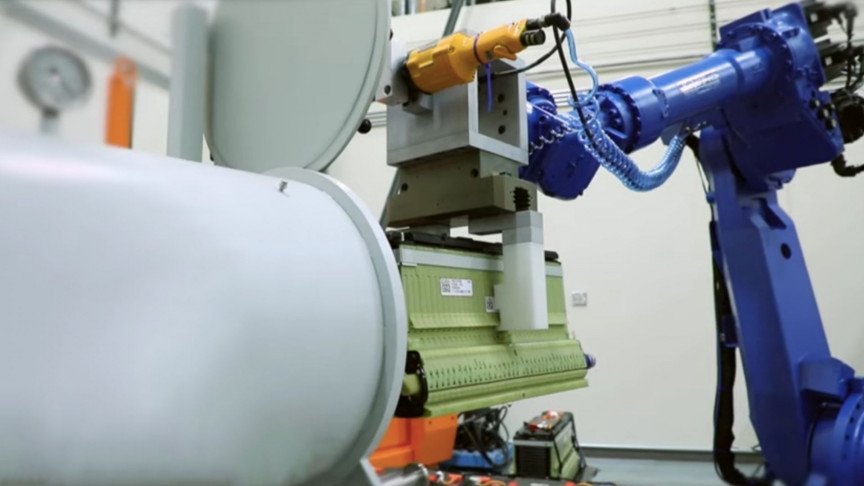
The robots swiftly remove bolts and other housing regardless of any remaining charge, whereas human operators must undertake an exacting, lengthy process to discharge used batteries before breaking them down manually.
Automated disassembly reduces human exposure to toxic chemicals found inside the batteries and high power levels that are approaching the 900-volt level in some newer vehicles.
The automated system can be programmed to access just the individual battery modules for refurbishment or reuse as stationary energy storage, or the batteries can be taken apart down to the cell level for separation and materials recovery.

Industry is not limited on the amount of batteries they can take into this process. It is estimated that in the time it takes in some processes to disassemble 12 battery stacks by hand, the automated system could handle 100 or more.
With the anticipated growth in EVs over the next two decades these automated robotic disassembly system will be better equipped to recycle the large lithium-ion battery packs.
This is a Businesswire Feed; edited by Clean-Future Team