Electrification of heavy-duty EVs is integral to decarbonization efforts, but vehicle components must be designed to handle more power while continuing to regulate operating temperatures.
A state-of-the-art thermal management system developed by the National Renewable Energy Laboratory (NREL) in collaboration with John Deere promises to significantly increase the power density of silicon carbide (SiC) inverters within heavy-duty EV applications.

Within heavy-duty applications, the power inverter is responsible for controlling the power flow between DC and AC electrical systems in order to run vehicle systems, accessories, and electric machines, such as motors and generators.Recent studies indicate that the improved design boasts a 378% increase in power density over the previous silicon-only inverters.
A common strategy for the thermal management in EVs is to run a fluid coolant parallel over the component’s surface to transfer heat and cool the system quickly.
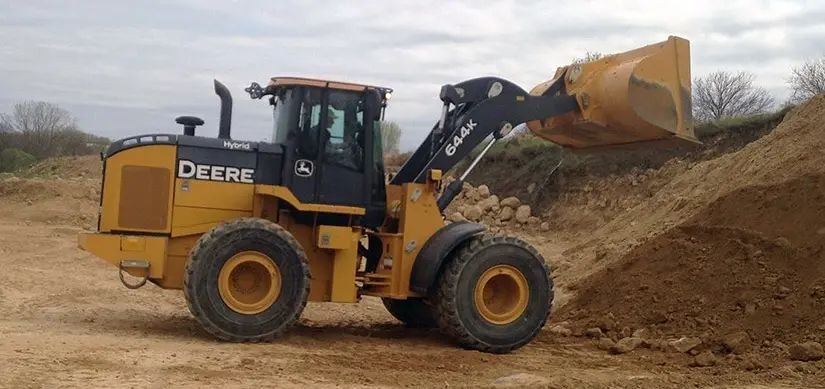
The advanced system designed at NREL incorporates perpendicular jet flow with mini-channel- and mini-manifold-based cooling systems to extract heat from the inverter and power module.
This design enables an impressive heat-transfer coefficient—as high as 93,000 watts per square meter per degree Kelvin (W/[m2-K]) which is over four times higher than current commercial systems.

The SiC inverter technology stands out among all competing technologies in terms of energy efficiency, fuel economy, performance, and system integration.
A high-efficiency inverter is a critical component necessary for environmentally friendly vehicle alternatives that reduce greenhouse gas emissions such as hybrid, full electric, or fuel cell vehicles.
This is a PR Newswire Feed; edited by Clean-Future Team