Ships that had been at sea for an extended period of time came to dock with hulls tainted with barnacles, seaweed, and other marine filth. This delayed the vessels—laborers had to scrub the vessels clean for days or weeks.

Sir Charles Middleton, comptroller of the British Royal Navy in the 1700s, came up with the novel notion of copper plating the ship’s hull below the waterline, which made the ship smooth.
Copper is still used on many ocean-going ships today, most notably as a component in certain distinctively red antifouling paints. This eliminates fouling and results in a smoother hull with reduced drag. This cuts fuel usage and carbon emissions. With less fouling, fewer potentially invasive marine organisms are transported throughout the world.
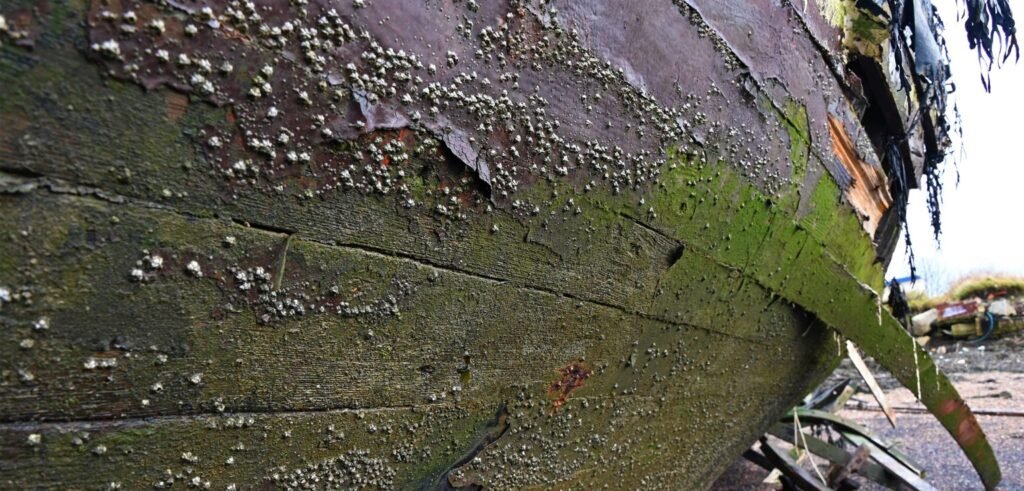
Yet with new regulations tightening emissions requirements, ship owners are taking hull coatings more seriously than ever before. The challenge is to find effective, sustainable coatings that don’t cost the Earth or leach heavy metals into the ocean.
Following in the footsteps of Middleton’s copper plates, innovations to combat fouling continue to emerge. Consider the textured coating inspired by sharks developed by AkzoNobel, a Dutch company. Instead than attempting to make a ship’s hull as smooth as possible, it emulated shark skin’s inherent roughness, which is naturally drag-reducing and antifouling.
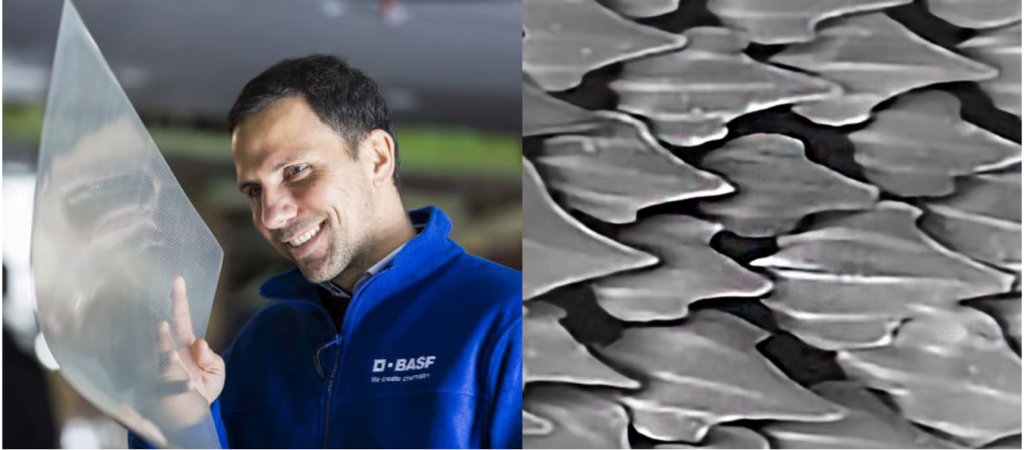
Such textures have successfully been applied to the bodies of commercial airplanes to minimize drag in the air, but AkzoNobel has yet to claim similar success in the water.
Other researchers are investigating the use of ultrasound or UV light to prevent marine creatures from clinging to hulls. Killing bacteria before they connect to the vessel might limit the production of biofilm, which barnacles and other stowaways cling to. The search for a perfect coating is still on…
Reference- New Atlas, Interesting Engineering, Clean Technica, Popular Science, Royal Museums Greenwich, Hakai Magazine, AkzoNobel PR